LEAN Manufacture Basic
Before you deeply enter into lean manufacturing, you first need to understand what value-added activities and non-value-added activities in manufacturing are.
Value-added activities: These activities are mandatory for manufacturing and are what customers are willing to pay for.
Non-value-added activities: These activities are not essential for manufacturing, and customers do not pay for them.
Now, let’s come to the point of lean manufacturing. It is a systematic process that reduces non-value-added activities, or waste, to achieve the goal of shortening the time to meet customer demands. Simply put, lean manufacturing means reducing waste. The basic principle of lean manufacturing is to eliminate waste in the production process, maintain a continuous flow of production, and ensure the perfect quality of the product to meet customer demand.
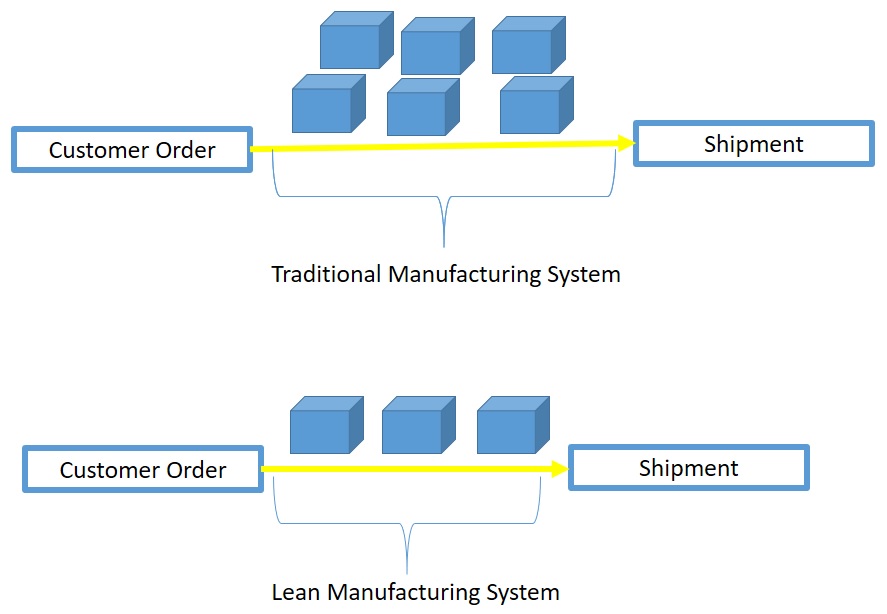
Now, you might be wondering about the benefits of implementing the lean concept in your factory:
01. Increase the productivity of the production line and improve product quality.
02. Reduce Work in Process (WIP) inventory.
03. Help identify and eliminate waste and problems in the production line.
04. Shorten the cycle time of operations and lead time.
05. Enhance the production flow of the production line.
06. Minimize the requirements for manpower, time, and space in production.
07. Improve visual management within the factory.
08. Minimize machine downtime to increase production availability.
09. Properly utilize all resources.
10. Promote sustainability, employee satisfaction, and profitability.
11. Properly organize the workplace.
12. Improve safety conditions throughout the factory.
13. Improve customer satisfaction and the level of service.
Here are some key tools of Lean Manufacturing. In the Lean Manufacturing section of this website, you will find detailed information about these tools (Some are already posted; others are still pending. Please be patient).
01. 5S
02. Kaizen
03. Kanban
04. Value Stream Mapping (VSM)
05. Total Productive Maintenance (TPM)
06. Just-In-Time (JIT)
07. Poka-Yoke (Error Proofing)
08. Heijunka (Level Scheduling)
09. Gemba (The Real Place)
10. Andon
11. Hoshin Kanri (Policy Deployment)
12. Takt Time
13. Seven Wastes
14. SMED (Single-Minute Exchange of Die)
15. Continuous Flow
16. Bottleneck Analysis
17. Root Cause Analysis
18. Cycle Time
19. Overall Equipment Effectiveness (OEE)
20. Visual Management System