Seven Wastes
Several wastes are often seen in lean manufacturing, which lead to DOWNTIME in the production line. These are also known as the Seven Wastes:
- Transportation waste
- Inventory waste
- Motion waste
- Waiting waste
- Over-processing waste
- Over-production waste
- Defects waste
If you want to memorize these seven wastes easily, just remember the word TIMWOOD, which stands for the below seven wastes. Sometimes, people add one more waste to this list, known as Skill-Set (non-utilized talent) waste. Let’s look at the details of these eight wastes:
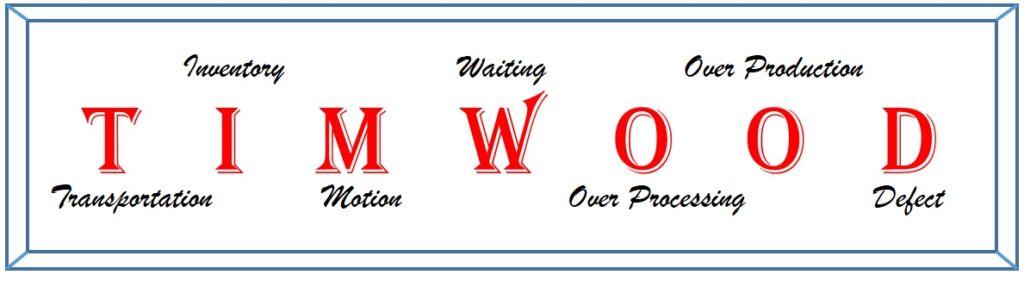
Transportation waste
Unnecessary movement of people, equipment, or materials affects the smoothness of production flow and can cause possible damage to products. One main reason for transportation waste is poor layout (large distances between operations). For example, if the cutting department is located in building A and the sewing or stitching department is in building B, and the distance between these two buildings is 200 meters, transporting materials between these departments is a waste. In lean manufacturing layouts, the cutting and sewing departments should be located in the same building and on the same floor to reduce this waste. Some advanced manufacturing factories place the cutting, stitching, and assembly lines on the same floor, which allows the process from cutting material to completing shoes to be done in a shorter time.
Inventory waste
Excessive inventory that is not necessary takes up valuable space and requires resources to manage it. Common causes of inventory waste include overproduction of products, waiting waste, and defects product inventory.
Motion waste
Unnecessary movement that can produce defective products is known as motion waste. This can also harm people and damage equipment. Poor process setup is one of the main reasons for this waste. Poor production planning, shared equipment and machines, and lack of knowledge of production standard operations are also common causes of motion waste.
Waiting waste
Waiting for people, materials, equipment, and information wastes production time and is called waiting waste. Operators waiting for materials is a very common scenario in shoe factories. The worst impact of waiting waste is unplanned downtime. Lack of communication and process control are also reasons behind this waste.
Over-production waste
Producing more than the customer needs, which causes excess inventory, is defined as over-production waste. Inaccurate forecasts and unstable production schedules are the main reasons for this waste. Sometimes, customers do not clearly describe their demand, which impacts the production schedule.
Extra processing waste
Adding extra processes in manufacturing that customers are not willing to pay for is known as extra processing waste. Poor communication and not properly understanding customer demand lead to this waste. Slow approval of manufacturing processes and human error also cause extra processing waste.
Defects waste
The production of defective products, which require either rework or scrapping that customers are not willing to pay for, is known as defects waste. Poor quality control at the production level is the main cause of this waste. Lack of operator awareness, process mistakes, or poor machines that need frequent repairs can also cause defects waste.
Skill-set waste
Skill-set waste is not originally included in Ohno’s seven wastes, but it is a valid waste commonly seen in shoe manufacturing factories. If you do not properly utilize the talent, knowledge, and experience of people, it is simply a waste of skills. To improve the organization, it is necessary to take proper action and plan to develop the skills of all people.