Bottleneck
A bottleneck in a production line is a point where the production flow is obstructed, causing delays and reducing overall output.
How easily can you identify the bottleneck point in a production line?
You can simply walk through the production line and try to find two key points:
01. Where the operator is either waiting for material or working very fast and then waiting for the next task. Near this operator, you can identify the bottleneck.
02. Where an operator takes a long time to complete their operation. In the latter case, there could be several reasons behind it, such as too much work being assigned to the operator, the operator not being skilled in that particular operation, or the operator being absent or on leave. Use the 5WHY method to identify the root cause of the problem.
If you don’t visit the production line, how can you find the bottleneck?
Data Analysis: Analyze production data, such as cycle times, production rates, and downtime records. Look for stages where the output significantly drops or where delays frequently occur.
Operation Breakdown Mapping: Create detailed process maps or flowcharts of the production process to visualize the flow of materials and identify potential bottlenecks.
Employee Feedback: Gather feedback from production line supervisors or operators who work on or near the production line. They can provide insights into where delays and inefficiencies occur.
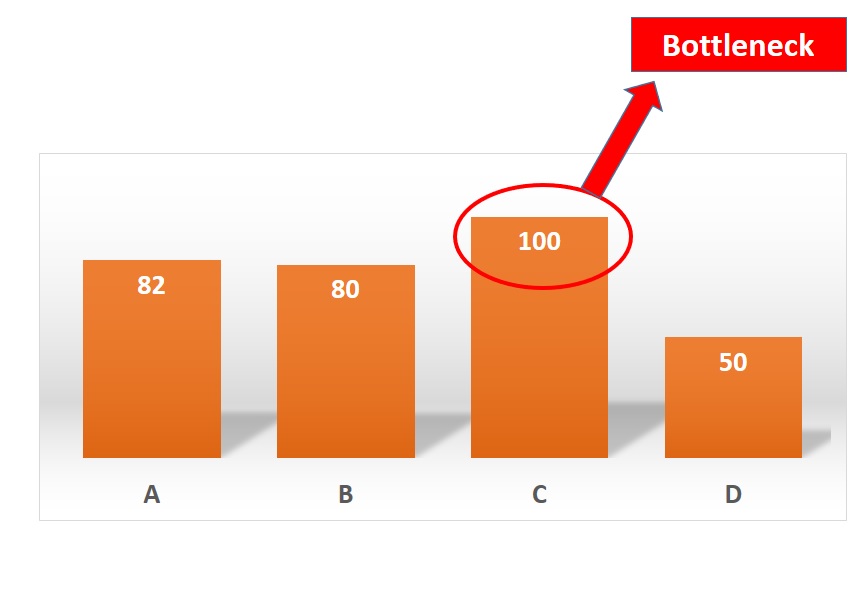
Let’s analyze this diagram. Given the operation times:
Operation A: 82 seconds
Operation B: 80 seconds
Operation C: 100 seconds
Operation D: 50 seconds
How to identify the bottleneck of this production line?
The bottleneck is the operation that takes the longest time to complete because it determines the pace of the entire production line. In this case, Operation C takes the longest at 100 seconds.
How does this bottleneck impact the production line?
Since Operation C is the bottleneck, it will slow down the overall production rate. All other operations will either have to wait for Operation C to complete, or they will finish their tasks early and then remain idle. Operation A and Operation B, while also time-consuming, are slightly faster than Operation C, meaning they will finish before Operation C and might end up waiting, leading to inefficiencies. Operation D is much faster at 50 seconds, which means it will consistently have idle time, waiting for the other operations to complete.
How to improve production line operator working efficiency?
Redistribute Work: If possible, distribute some of the work from Operation C to the other operations, particularly Operation D, to balance the workload.
Parallel Processing: Consider introducing parallel operations for Operation C to handle the workload more efficiently and reduce its impact as a bottleneck.
Process Improvement: Investigate whether Operation C can be made more efficient through process improvements, automation, or better resource allocation.
In summary, Operation C is the bottleneck in this set of operations. To improve the overall efficiency of the production line, focus on optimizing or balancing Operation C with the other operations. Using the above technique, you can easily identify the bottleneck in the production line and increase production capacity if you follow the suggested improvements.